蔡坤釗 呂文豐 張中興
核能研究所燃材組
摘 要
鎳基合金X-750 為核反應爐零組件的材料之一,核一廠於第24 次大修(EOC-24)期 間,發現3 只燃料匣鎖緊裝置螺栓斷裂,為釐清該螺栓的斷裂原因,將受損螺栓部份斷 件(螺帽)送至核研所進行熱室檢驗與破壞分析。
本報告對斷裂螺栓進行之熱室檢驗,包括化學成份分析、液滲檢測、微硬度量測、 金相檢驗、破斷面觀察、及掃瞄式電子顯微鏡(SEM)斷面分析。
檢驗結果顯示,斷裂螺栓材質為鎳基合金X-750;螺栓沒有輻射脆化及加工硬化效 應;龜裂發生在或接近螺桿5/16"縮減為1/4"之頸部圓角位置;龜裂起源型態為穿晶模 式,繼而以沿晶模式貫穿螺栓。綜合螺栓SEM 斷面及金相分析結果,確認沿晶應力腐 蝕龜裂為此破壞機制;螺栓斷裂的可能原因為不當外力促發應力腐蝕龜裂。
關鍵詞:燃料匣鎖緊裝置螺栓、破壞分析、鎳基合金、X-750。
壹、 前言
一、鎳基合金X-750
現今輕水式反應器(LWRs)所使用的鎳基合金,包含合金 600、690、718、A-286、 及X-750 等。這些合金是為特殊高溫環境的使用而設計,具有較一般不鏽鋼材料優異之 高溫強度、潛變抗性、耐熱疲勞、及耐蝕性。合金X-750 為一析出硬化型合金,熱膨脹 係數較其它高強度合金鋼低;因應核電廠運轉環境,其成份與熱處理都施以最佳化調整 與處理。然而經過核電廠長期使用後,部份合金X-750 材料組件發生損壞,此情況在國 內、外均有類似的報導,核一廠此次受損的燃料匣鎖緊裝置螺栓組件材料,即是所述 X-750 合金;這些損壞案例主要歸因於沿晶應力腐蝕龜裂(Intergranular Stress Corrosion Cracking;IGSCC)[1]。對於合金X-750 的主要顯微組織及熱處理,簡單描述如下:
Inconel X-750(UNS NO7750)的主要相及元素包括有形成沃斯田體(γ)基地相的 鎳、鐵、及鉻等元素;增加合金高溫強度的鋁、鈦、鈮;主要強化相(γ')為Ni3(Al,Ti), 次要強化相(γ")為Ni3Nb;碳化物主要為高溫形成的MC 型碳化物及隨後熱處理而析 出的M23C6 型碳化物[1],MC 碳化物中的M 主要為鈦及鈮,M23C6 型碳化物中的M 主 要為鉻;在ASME SB-637 的規範的主元素與ASTM 有相同的成份規格,詳細元素規格 如表1 所示[1~2]。
二、X-750 熱處理
鎳基合金針對高溫環境所施作之熱處理,包括三階段,分別為固溶處理(solid solution)、中間處理或安定化處理(stabilizing treatment)、以及析出硬化處理(precipitation hardening treatment)。如前段所述,γ'和γ"為X-750 主要之強化相,不同的熱處理方式會 影響到γ'相的析出強化效果,包括γ'相的體積、γ'相的粒子大小、γ'粒子與γ基材間因晶格 差異(misfit)所存有的共格應變(coherent strain)之界面能(interfacial energy)。對碳化物而 言,藉由熱處理可使M23C6 碳化物在晶界上呈半連續狀析出,晶界M23C6 碳化物可提供 強化效果,也有助於防止IGSCC;MC 碳化物對強化效果的貢獻很少,但因生成該碳化 物時,間接減少了基材的碳,使M23C6 碳化物的生成相對減少,間接影響到機械性質及 抗IGSCC 的功效[3~6]。
X-750 在ASTM B637 的標準規範中分為3 種熱處理方式[1~2],而其中第3 種(Type 3)稱為HTH的熱處理方式,其熱處理條件是於1107°C 下持溫1 小時後快速冷卻到704°C 的時效溫度,保持20 小時後急冷到室溫,這種一階段方式較兩階段時效熱處理的方式 有較佳之抗SCC 的效果,其機制尚有待釐清,除該熱處理所有利於晶界之M23C6 碳化 物生成外,部分論述理由如下:
(一)高溫的退火處理會使MC 碳化物的溶解度增加,有利於時效階段M23C6碳化物的析 出,而晶界上M23C6碳化物有助於防止IGSCC,目前此種一階段的時效處理可於晶 界產生最多的不連續及半連續的M23C6碳化物[1]。
(二)在一階段的析出硬化處理後,產生較細的粒子,在變形過程中,差排(dislocations) 可以剪切(shear)通過;而二階段的均質化處理的X-750材料,在850°C 時,形成較粗 大的γ'粒子,差排不易剪切(shear)通過,相反的累積成微孔洞,但同時晶界上產生 更多γ'強化相,而較少生成M23C6碳化物,雖然仍有高強度,但有較差之抗IGSCC 效果。
貳、 實驗步驟與實驗設備
兩斷裂螺栓試片從核一廠運送至核研所後,先在清水中以超音波振盪去除粉塵及鬆 散的沈積物,以降低輻射粉塵污染;再進行目視檢查以檢驗受損螺栓之外觀及斷面;隨 後以液滲試驗確認微裂分佈及其位置;以SEM(Hitachi S-4800),進行斷面分析以分析斷 裂面型態與破損機制;完成破損面觀察後,製作剖面金相,觀察破裂源附近是否有異樣 雜質與缺陷;為明瞭硬度之變化情況,微硬度量測是以300g 荷重、負載時間為10 秒在 金相試片上進行量測;另一方面,也使用感應耦合電漿原子放射光譜儀(Jobin Yvon JY38S)來確認成份;此外,對未照射之新螺栓進行扭斷模擬試驗,經由微硬度量測及 SEM 觀察,來比對斷裂螺栓的破裂行為與破壞機制。
參、 結果與討論
一、螺栓A 之破斷面及金相觀察
圖1 為斷裂螺栓A 之螺帽斷面及側面照片,初步的目視檢驗研判,平坦之區域A, 可能為斷裂之起裂源(initiation site);區域B 為裂紋穩定成長區域;區域C 凸起之螺桿 餘肉,為裂紋最終失穩(unstable)快速前進所造成;外觀經液滲檢驗確認沒有其它裂紋。
圖1 螺栓A 斷面區域A、B、C 之細部放大,分別為圖2~4 之SEM 觀察及圖5~7 之剖 面金相。圖2 中可見破斷面主要是沿晶(intergranular)破斷,確認圖2 的區域(圖1 區域 A)為斷裂的起裂位置,照片上為穿晶與沿晶的混合模式;該區域出現腐蝕沈積物(圖5 剖面金相可以觀察到此明顯的腐蝕氧化層);圖3 中整片區域都是沿晶斷裂,斷面氧化 物較圖2 要來得少;圖4 研判為最後斷裂區域,沒有發現渦孔(dimples)等延性破斷(ductile fracture)表徵,而是沿晶龜裂與穿晶劈裂的混合型態。圖5 是圖2 之穿晶剖面金相,顯 示穿晶破裂源;圖6 為圖3 及其附近位置之剖面金相,從圖中可以觀察到氧化層厚度隨 著遠離起裂源而減少,從氧化層的厚度變化可知裂紋形成的先後,再次印證圖1 的區域 A 為螺栓A 的起裂源;圖6 上存有斷面延伸的二次裂紋,裂紋被氧化物所填滿,二次 裂紋為沿晶應力腐蝕龜裂的一項表徵;圖7 為相對於圖4 位置的剖面金相,其斷面幾乎 沒有氧化層,顯示該區域(圖1 區域C)為最終斷裂位置,斷面為脆性沿晶破裂與劈裂的 混合形貌。可以推論初期的裂紋生長過程為晶界先被腐蝕弱化後,沿著弱化的晶界生 長;一旦裂紋生成到某階段後,IGSCC 的斷裂進入裂縫成長階段,最後螺帽所殘留之 未破斷部分無法支撐整體應力而產生沿晶破裂與劈裂的混合形貌。
二、螺栓B 之破斷面及金相觀察
目視相片上,螺栓B 之斷裂面沒有明顯的凸起之螺桿餘肉區域,圖8 為螺栓B 的 SEM 破斷面,圖上標示了D、E、F 區域,分別代表不同破斷面的形貌;圖9~11 和圖 12~14 分別為圖8 螺栓B 的區域D、E、F 之斷面細部放大圖和剖面金相;圖9 的區域 為明顯的氧化層,研判為斷裂的起裂位置;圖10 為圖8 的E 區域的細部放大,可以觀 察到整片區域都是沿晶斷裂,氧化減少,且明顯的有二次裂紋存在;圖11 為圖8 區域 F 的放大,同螺栓A 一樣,沒有發現渦孔等延性破斷表徵。
圖12 為圖9 的剖面金相,該區域為穿晶模式,且可以觀察到表面的氧化層;圖13 的區域為沿晶斷裂,表面氧化層減少,並有二次裂縫的存在;圖14 為圖11 的剖面金相, 該區域為穿晶模式,可以觀察到表面的氧化層。從以上比較得到,兩外側區域表面有明 顯的氧化層且為穿晶的模式,可以推論且螺栓B 的斷面形成為多處起裂源造成。
此外,螺栓B 剖面金相顯示除上所述之主裂紋外,在頸部處亦發現一道從表面延 伸的裂紋如圖15 所示。由金相圖中,裂紋外側氧化較嚴重且較寬,可推測裂紋由外部 向螺栓中央沿伸,此裂紋開口(crack opening)約為5μm,小於液滲檢測之25μm 可分辨 率,該起裂源為穿晶模式,在圖16 的放大中,推測可能有析出物剝離,圖17 為裂縫中 段,該區域裂紋填滿氧化層;部份中段裂紋形成分離的氧化界面如圖18 所示;圖19 為裂紋末段,形成局部有析出物之現象,由此可以推論裂紋的生長過程為晶界先被腐蝕 弱化後,裂縫在一較大應力之作用下,沿著弱化的晶界生長,裂縫生長過程中,氧化持 續於裂縫末端沿晶界成節點的生成。
正常情況下,螺桿頸部應有明顯之應力集中,但是螺栓B 顯示斷面受的應力大於 螺桿頸部集中之應力;此意謂螺栓在斷裂前,主軸應力(principle stress)為偏離垂直位置 而造成應力重新分佈,導致斷面處的應力大於螺栓頸部區域集中之應力。從圖15 中可 以觀察到螺栓A 斷裂面與螺栓水平截面幾乎平行,而螺栓B 裂紋與螺栓水平截面約有 20°夾角,這代表兩件螺栓所受之最大應力方位角度不同;此次之大修,鎖緊裝置螺栓 除了發生斷裂外,還有四個鎖緊裝置發生彎曲(未斷裂),鎖緊裝置在彎曲狀態,螺栓的 最大應力就會偏離螺栓頸部區域。彎曲的燃料匣鎖緊裝置容易在燃料匣移位或固定時受 到撞擊,使螺栓承受額外的撞擊應力而導致受損。在螺栓B 沿晶龜裂的區域內發現有 小部分的穿晶龜裂區域(圖13),合理的解釋是彎曲的鎖緊裝置受到不明原因之撞擊,且 瞬間撞擊的應力大於X-750 降伏應力(因龜裂已使晶粒破裂),因此使得局部裂紋為沿著 瞬間撞擊之臨界分解剪應力方向,以穿晶模式成長,而不是晶界腐蝕後的沿晶斷裂。
三、硬度量測與化學成分
螺栓A 與B 在距離斷面0.2mm 處的平均硬度值分別為373 HV 與377 HV,螺栓A 與B 遠離斷面區域的平均硬度分別是372 HV 與383 HV。另一方面,未照射螺栓試樣 的平均硬度為377 HV,螺紋區域的平均硬度為398 HV,螺紋區域平均硬度較高是加工 造成的硬化效果。因為照射前後硬度沒有改變,顯示螺栓A 與B 沒有明顯的中子輻射 脆化效應。另外,以感應耦合電漿原子放射光譜儀分析化學成份,其結果如表一所示, 確認成份為合金X-750。
四、熱處理、製造過程及使用環境的影響
依照核一廠所提供的設計資料,熱處理的程序為於2000~2050°F 持溫5~10 分鐘後 快速冷卻,以進行固溶處理,而後於1275~1325°F 持溫20 小時進行時效處理。該熱處 理方式與文獻之HTH 熱處理[2]差異在於固溶化處理時間為1 小時,在GE-Hitachi 為 EPRI 所提的BWRVIP-218 報告中[1],該熱處理具有抗IGSCC 的功效。
未照射的燃料匣鎖緊裝置螺紋經扭斷,測得最終扭力矩為1076 in-lbf,其斷面觀察 到指向軸心之放射狀山脊(ridge)斷裂形貌。此與螺栓A 與B 之斷面形貌完全不同,且斷 裂位置為螺紋區域,所以斷定螺栓A 與B 的斷裂不是扭力過大造成。
五、小結
螺栓A 與B 斷裂的區域在頸部區域,以及斷面沒有指向軸心的放射狀山脊形貌, 所以確認螺栓A 與B 的破損不是因為鎖緊時扭力過大而造成。螺栓A 與B 斷裂面上沒 有渦孔延性破壞形貌(此型破壞需大量塑性變形),反之是微量變形之沿晶脆性破壞,因 此確認螺栓A 與B 所承受的應力,在腐蝕作用下,已達到(或超過)應力腐蝕龜裂所需之 應力門檻。螺栓A 為單一起裂源,初期的裂紋生長過程為晶界先被腐蝕弱化後,裂紋 沿弱化晶界進行成長(IGSCC 龜裂),最後因螺帽殘留之未破斷部分(ligament)無法支撐整 體應力,而產生沿晶破裂與穿晶劈裂的混合破壞。而螺栓B 為多處起裂源造成,且額 外外力使主軸應力偏離軸心垂直位置,造成應力重新分佈,導致斷面處的應力大於螺栓 頸部區域集中之應力,此時裂縫沿主應力垂直方向傳播。
肆、 結論與後續研究
根據所完成的目視、液滲、SEM、金相與微硬度分析等結果分析顯示,螺栓沒有微 觀明顯的材料缺陷,硬度亦屬正常,螺栓主要斷裂模式為IGSCC 龜裂,穿晶模式只發 生在斷面起源與最後斷裂區域。由剖面照片觀察發現,螺栓A 在應力集中之螺栓頸部 有穿晶龜裂,顯示此處所受的應力有大於材料降伏應力的可能(在充分之應變率條件)。
螺栓B 的斷面距螺栓頸部1.5mm,這代表燃料匣鎖緊裝置已經彎曲或可能是燃料匣鎖 緊裝置螺栓鎖緊時未對準(mis-alignment),因而造成斷面附近所受的應力大於螺栓頸部 集中之應力。根據上述所有分析結果,本破壞分析得到以下之結論:
(1)螺栓A 破壞機制為IGSCC,主要肇因為螺桿尺寸由5/16"縮至1/4"之頸部區域所 受應力過大。
(2)螺栓B 破壞機制為IGSCC,主要肇因可能為燃料匣鎖緊裝置彎曲或是鎖緊裝置 螺栓鎖緊時未對準,因而造成作用在鎖緊裝置螺栓之應力重新分配,於距離應力 集中1.5 mm 處形成更大之應力,造成螺栓斷裂。
(3)額外的碰撞使IGSCC 沿晶斷裂轉為穿晶斷裂,短期加速螺栓裂紋成長。
後續之研究方向如下:
(1)針對新發生斷裂燃料鎖緊螺栓作分析及檢驗,確認可能的外力來源及破裂行為。
(2)利用有限元素法進行應力分析,以瞭解螺栓之應力分佈及再分佈,並模擬燃料 挪移作業時螺栓所受到之外力大小。
伍、 參考文獻
[1] BWRVIP-218: BWR Vessel and Internals Project, Alloy X-750 Characterization Study. EPRI,Palo Alto, CA, 2009, 1019070.
[2] ASTM B-637-98, “Standard Specification for Precipitation-Hardening Nickel Alloy Bars, Forgings, and Forging Stock for High-Temperature Service,” ASTM, 1998.
[3] S.Floreen, J.L. Nelson, “The Effects of Heat Treatment and Composition on the Stress Corrosion Cracking Resistance of Inconel X-750”, Met. Trans., 14A, 1983, 133~39.
[4] R. Bajaj, W. J. Mills, M. R. Lebo, B. Z. Hyatt, and M. G. Burke. “Irradiation-assisted stress corrosion cracking of HTH Alloy X-750 and Alloy 625”, NACE, Vol. 2, 1995, 1093~1107.
[5] R. Ballinger, C.S. Elliott, S. Hwang and J. Prybylowsky, “The effect of thermal treatment on the fracture properties of alloy X-750 in aqueous environment”, EPRI CR , 1993, 102~437.
[6] Anders Jenssen, Pål Efsing, Johan Sundberg, “Influence of heat treatment, aging and neutron irradiation on the fracture toughness and crack growth rate in BWR environments of alloy X-750”, Proceedings of the 12th International Conference on Environmental Degradation of Materials in Nuclear Power System, TMS (The Minerals, Metals & Materials Society), 2005, 73.
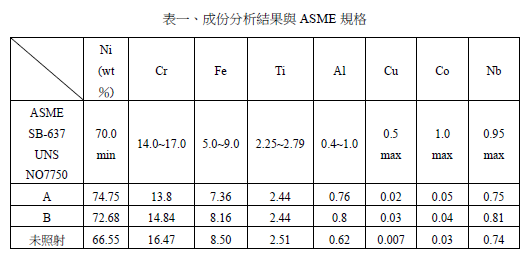
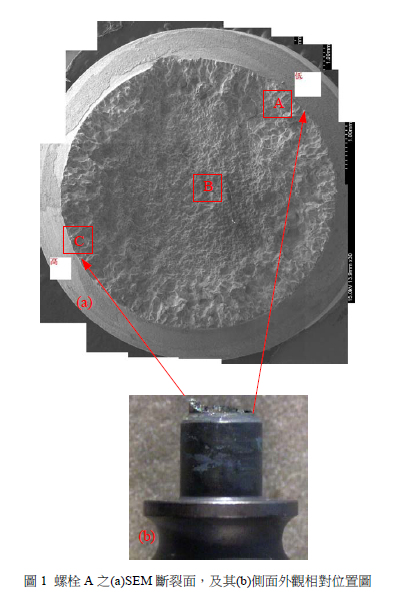

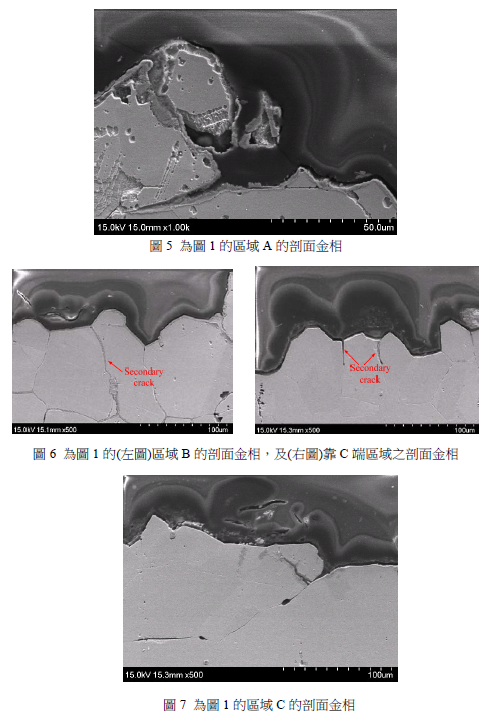
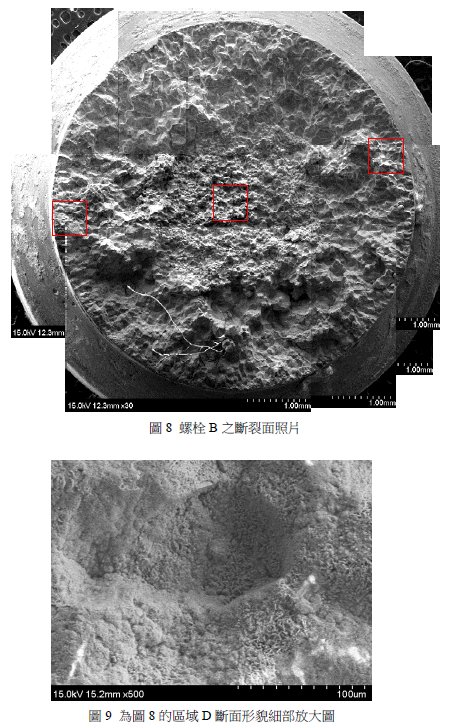
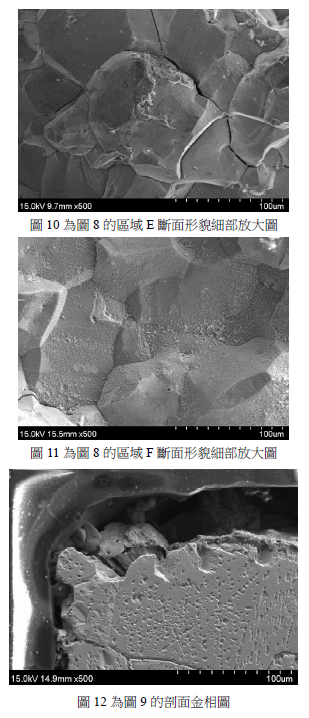
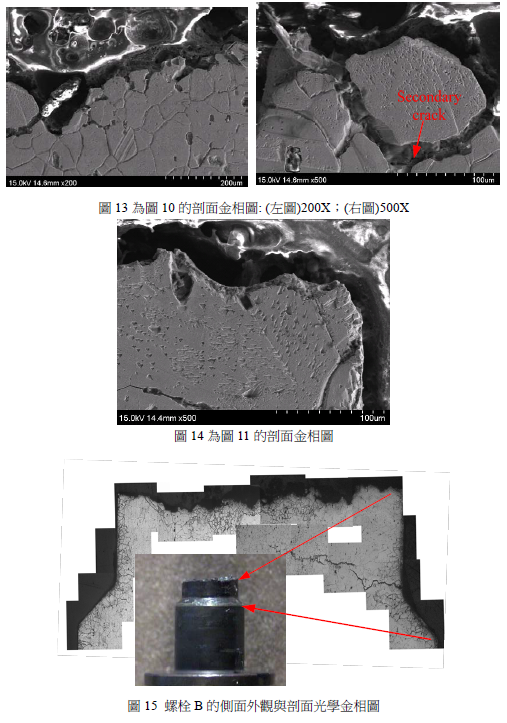
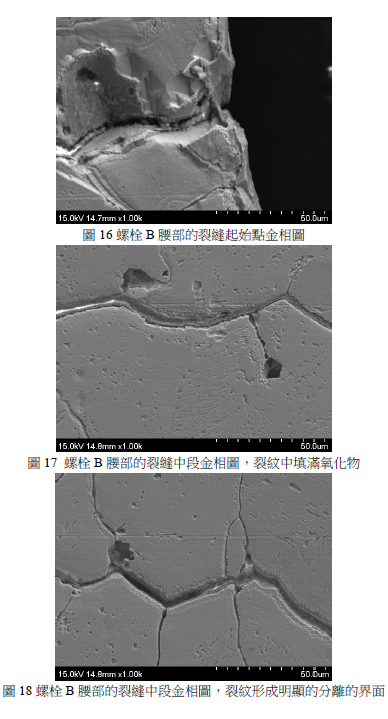
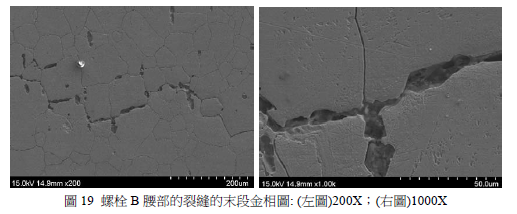